Reference : small 2013, 9, 107-114
Authors : Li Jiang and David Erickson
Authors : Li Jiang and David Erickson
Facile methods to guide flow without fluid modifications or integrating on-chip elements would minimize expense and fabrication complexity. The authors created a simple device that passively pumps flow at room temperature (RT) and actively valves flow based on photo-thermal heating, thereby eliminating the need for external pumps, integrated valves or complex fabrication steps.
PNIPAAm was grafted on polydimethylsiloxane (PDMS) microfluidic devices via UV-mediated polymerization [Schneider et al., Langmuir 2011, 27, 1232]. PNIPAAm is a temperature-responsive polymer: the chain conformation changes from coil-like (expanded) to globular (compacted) at its lower critical solution temperature of 32 °C. Thus, the modified microfluidic channels were hydrophilic at RT and therefore passively pumped flow via capillary action. When a specific region was heated to T>40 °C, it impeded further flow. Light produced from a projector (Krishnan et al., Lab Chip 2012, 12, 613) was focused onto the chip, where a thin carbon black layer above the channel structure converted it into heat, valving flow at that location (first figure, A, B).
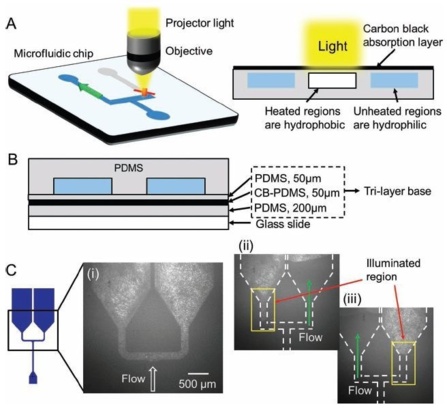
A bifurcating microfluidic design was presented, where the inlet channel splitted into two large chambers. Each chamber represented a separate step of a multistage process. In step 1, projector light is incident on the left or right channel, heating that region and valving off the flow, while flow continues down the adjacent hydrophilic path. In step 2, light is removed, allowing liquid to penetrate into the previously closed chamber (first figure, C).
The characterization of the flow inside the channels was achieved by optical microscopy. Each test channel (0.2 × 1 mm cross section) was placed on a hotplate. A droplet of de-ionized water was placed at the inlet and the liquid meniscus position was tracked (second figure, A). It was revealed that the flow rate steadily decreased with increasing T up to 40 °C, after which it became very low (second figure B, C). A closer examination above 45 °C showed that the flow rate slightly increased with T. This was attributed to the evaporation and condensation of the liquid (second figure, D). From RT to 40 °C, flow could be tuned at will to a specific speed. The authors were able to achieve suppression of flow from 4 μL/min at RT to 0.1 μL/min at T=40 °C.
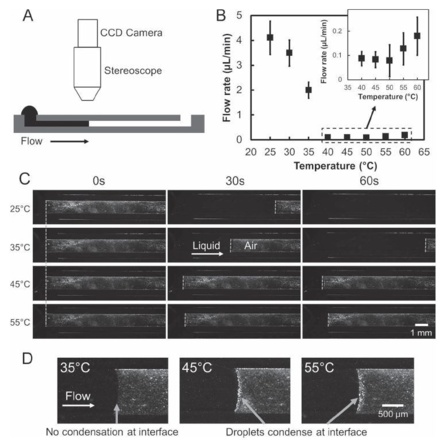
The projector setup was further used to demonstrate light-based flow manipulation. Successive light OFF and light ON cycles corresponded to water progression and stop of the flow, respectively (third figure, A). The fluid displacement and velocity through such an ON/OFF series was also shown (third figure, B). Moreover, the normalized switching speed of the device was measured (third figure, B). These results, along with in situ T measurements by means of fluorescent imaging [Erickson et al., Lab Chip 2003, 3, 141] demonstrate that the surface of the channel responds quickly (~4s) to the T changes and that the system response is substantially governed by the heating time.
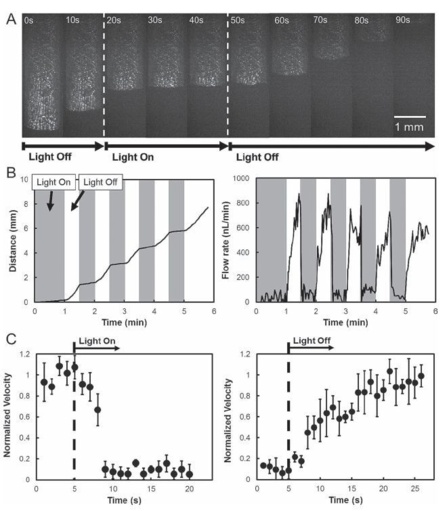
The feasibility of using solar-thermal energy to control such a device was discussed. The intensity of the incident projector image was calculated to be ~1.5x104 W/m2, about an order of magnitude higher than solar intensity (103 W/m2). The authors suggested that either increasing the area that light is incident on the chip or utilizing a lens could provide the desired total power from sunlight and achieve the temperatures necessary for valving.